FEA shortens the Design Cycle for Thermal Radiation Detector System for Power Plant
Case Highlights: Client :
- The customer is a leading Detection Systems solution provider.
- The customer is into Designing and Manufacturing of Thermal Radiation Detection System for Plants.
Technology / Software Used: FINITE ELEMENT ANALYSIS
Business Requirements / Challenges:
- Providing a Solution to Industry is one of the most critical requirements due to the High Severity level of the Domain.
- Due to high competition in the market, the customer satisfaction expectations are always high in terms of Delivery which in turn demands for shorter Design Cycles.
- With these expectations, it becomes essential to focus on Designs which can be readily used with fewer number of Prototype Testing
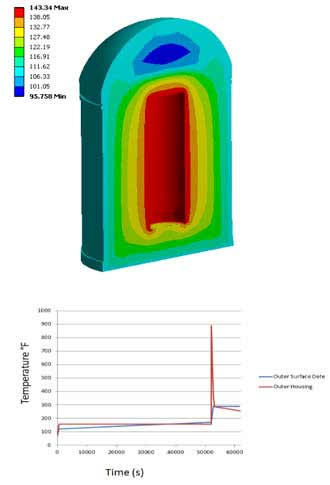
Solution:
- A detailed three dimensional Finite Element Model was constructed for Thermal Qualification analysis of the Detector Assembly.
- The software used to perform Thermal analysis was ANSYS v13.0 Mechanical Module. The model design and geometry was done using Solid Works Software.
- The analysis was performed to determine the maximum temperature of the detector by applying the Thermal Load Curve at the outer Housing which is having a very high peak for a very small duration. The objective was to find out the maximum temperature at the Detector when this peak temperature occurs at the outer Housing.
Benefits:
- The Filtration Area optimization simulation which was done with the help of ANSYS Design Modeler and Professional NLS, provided a technically feasible solution with increased output and also reduced the number of prototype as the first prototype gave a satisfactory performance.
- Assessment by FEA methodology shortened the Product Development Cycle by significant amount.