Stress Analysis and its Different Aspects
Posted by Bhaumik Dave on April 4th, 2013
Stress Analysis is an industrial testing method based on calculation of mechanical stress, strain, and related deformations. This type of analysis is often performed as a final part of more complicated multi-field analysis of elector-mechanical devices. In an elaborated way, Stress analysis is a computational method for application of load on a structure for determining its resulting response.
Stress analysis is often used a counter evaluation of structural analysis on basis of fatigue assessment and failure analysis process.
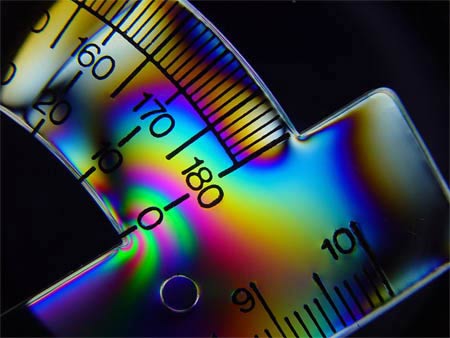
Stress analysis services are often used in different industries like Aerospace, Marine, Automobiles, Oil and Gas, Security and Defense, Railways, Medical and Healthcare, Construction, and Manufacturing. Stress analysis calculations are often used for determining stress and strain level of industrial structures, Marine components, Sub-sea components, rail, aircraft, and aerospace, nuclear components and structures, etc. This calculation is done by Stress Analysis Software like SolidWorks, Ansys, etc, which are known for their accuracy and authenticity.
Different features are found in stress analysis modules. Some of the prime features are:
- Anisotropic stretch properties
- Dispersed and rigorous loading
- Plane stress, plane strain
- Magnetic and electric forces and thermal stresses
Advantages of Stress Analysis Services:
- Finest FEA solutions for product design and growth
- Domain expertise of thermal & structure stress
- Fewer errors means no product failure
- Enhanced features and competitiveness
- Budget price solutions
- Exact calculation of deflection, strain, distribution of loads
The objective of stress analysis is generally to decide if the element or assortment of elements, commonly referred to as the structure, behaves as preferred under the agreed loading. For instance, this can be managed when the resolute stress from the functional force(s) is less than the tensile yield strength or under the weariness power of the material.
Stress Analysis may be performed during classical numerical techniques, logical mathematical modeling or computational simulation via new testing techniques, or a combo of techniques.
The measures quantities are considered in megapascals (MPa) or gigapascals (GPa) or in imperial units, pounds/ square-inch (psi) or kilopounds-force/ square-inch (ksi).
The Method of Stress Analysis:
The analysis of stress process within a body entails the willpower at all points of the body of the scale of 9-stress components. In other way, it is the willpower of the interior allocation of stresses. An option technique used in stress analysis is the purpose of the interior allocation of strains.
Professionals can build a part for serving a function while reducing the quantity of material used to make it for reducing the cost. To make sure that this specific part can work as required without breaking, these parts must be tested on the quantity stress it can take. Within SolidWorks Stress Analysis, an individual can create a part with a specific material or shape and perform a stress analysis of the concerned part.
The main part of analysis includes fixing the nature of loads acting on a structure, including tension, density, trim, torsion, winding or an amalgamation of some of these loads. When force is applied frequently almost all materials will get ruptured or failed at a lower stress than they should act likewise under a stable shape load condition. The analysis process to determine stress under these specific cyclic load conditions is called fatigue analysis and it is often applied for determination of stress level in an aerodynamic structural system.