How efficiently and quickly can a design engineer generate a valve assembly?
Posted by Rohan Belhe on February 10th, 2017
A gate valve manufacturer in Europe was able to reduce 40% of the manufacturing time and yet was able to design the gate valve assembly at a reduced overall cost which could accommodate fluids at different temperatures. Now this is quiet contradictory to the popular idea that quickly made products often lead to compromising quality. However, the manufacturer luckily had a good deal of design engineers and specialists equipped with technology working for him in optimizing the design and reaching the solutions quickly.
Today, even with the fastest methods to solve the problems, it would take considerably fair amount time and yet reach a conditional solution. A research or design engineer cannot rely and put their signature on drawings based on such decisions for accurate designing of components. So how exactly was the European manufacturer catered with such fine outcome?
For the sake of accuracy and real-time effects, most modern engineers used Finite Element Method – FEM, commonly referred to as Finite Element Analysis, through ANSYS NLS 14.5 for testing. This same method was employed to analyze designed model of gate vale assembly, before it was manufactured. Widely, FEA is used to test the component through simulations for calculating the real time effects on the component. Obtaining optimized geometrical solutions and solving flaws in designs quickly depends a lot on the productivity of the FEA software used and the hands on expertise of the engineer operating it.
How FEA fastens the process?
A typical gate valve assembly is made of metal comprising other components like hand wheel, seat, body of the valve, disc etc. Body of the valve, gate stem and slab gate are the most critical component to be analyzed for safety and performance validation. These components are often subjected to high stresses resulting due to high pressurized fluid flow. Valves, as such, are required to be designed to withstand the high internal pressure and cyclic loads to avoid the development of cracks that ultimately lead to early failure. The structural behavior of valve components can be quickly assessed for stress and deformation through finite element simulations.
The provision of applying real world boundary conditions such as loads, internal pressure and component material within the FEA tools like ANSYS Mechanical, enables the manufacturer to obtain meaningful results on stress generation, heat flux and effects of vibrations. Through fatigue life estimation, the engineer can quickly identify the useful life of the valve assembly and establish accurate warranty and servicing schedules. What makes this process quick is the ability to utilize single CAD model across all the tests, requiring no special equipment or test benches to obtain the results. On the contrary, physical tests consume considerable product development time, requiring measuring tools, testing equipment and an experienced resource to carry out the tests accurately.
Despite the problems associated with physical tests, FEA cannot be considered as a gold standard for testing, it is however a complimentary tool that helps the engineer to reduce physical trials and associated costs. A well defined FE-model with accurate boundary conditions can yield meaningful results, which can be applied for physical tests for final validation.
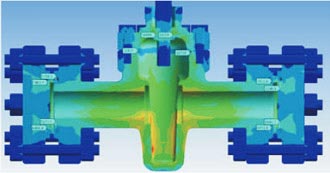
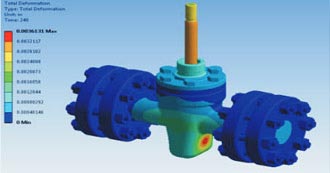
Overcoming the challenges in analysis through FEA
Coming back to the case of European manufacturer, since the engineers used software based approach; most of the time needed to spend on developing prototypes and conducting physical test was reduced. This eliminated 40% of the time required during usual product development stage. FEA also helped the manufacturer to reduce the cost of prototyping trials. Virtual FE model allowed the engineers to quickly change the design parameters and test the valve assembly for different applications and environmental conditions. Also, the results of stress concentration enabled design optimization through amendments in dimensions to achieve a safe design.
How helpful is an FEA Specialist?
Broadly speaking, an FEA specialist along with a design engineer is a valued proposition for product development stage. Results of FEA reports help the engineer in understanding the critical aspects of product design and predict failure conditions for real-world scenario while working in virtual environment. These results aid in design optimization of design and make the product more efficient. Various types of stresses and corresponding changes are examined to extreme conditions and the engineer can experiment with numerous sets of design to achieve an optimized design.