Design Optimization of Breaker Plate in Extrusion Machines
Challenges:
- Identify maximum number of holes for each given hole size
- Maintaining sufficient edge to edge gap between the holes to avoid dimensional irregularity due to deformation
Software Used: ANSYS Professional NLS 14.5
Solution: For given sizes of holes, the parametric model was developed using ANSYS CAD tool to identify maximum number of holes that can be drilled on the breaker plate. A followed stress analysis was performed to evaluate the deformation values for the breaker plates of different sizes of holes.
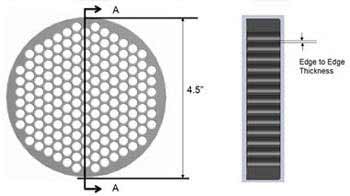
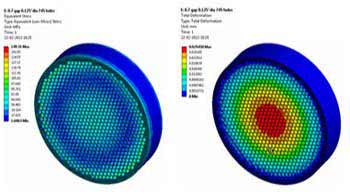
Breaker plates are essentially required in extruders to cover filter screens, and provide uniform melting and mixing of the polymer before entering the die. The number of holes in breaker plates has a direct impact on the time required for the forming process.
A leading extrusion machine manufacturer approached Hi-Tech to re-engineer the breaker plate, by increasing the number of holes of different sizes for a given design space. The customer also needed to analyze the optimized breaker plate design for stress distribution and subsequent deformation.
Solution:
Hi-Tech’s engineering team developed optimized breaker plate design with maximized number of holes of different sizes. Providing three different hole configurations for a given break plate geometry, the optimized design was also evaluated for stress distribution and deformation.
The edge to edge thickness between the successive holes was also crucial, to avoid excessive deformation due to stress generation. With consecutive iterations considering the different parameters, three optimized breaker plate designs were proposed possessing maximum number of holes as well as maintaining the stress and deformation values within the allowable limits.
Benefits
- Increased productivity from the extrusion machine with optimized breaker plate
- Reduction in time required for plastic forming
- Alternative breaker plate configurations with different hole sizes to suit specific applications
- Decreased the time required to perform prototyping tests